Promeco Densifying Extrusion Systems
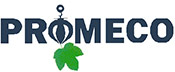
Promeco Densifying Extrusion Systems
Simple, flexible systems for densifying plastic waste
The PES (Promeco Extrusion System) is ideal for reprocessing a wide variety of flexible and rigid plastics from post-industrial and post-consumer sources, including:
Plastics (PE, HDPE, EPS, PP, PVC)
Mixed plastics and plastics contaminated with other materials including paper and cardboard, textiles and wood
Plastics with up to 20% moisture
The PES densifier operates continuously and automatically. After preliminary shredding, scrap material goes into a holding bin with two metering screws that feed material to an inclined vibrating table that guides the scrap into the open feed throat of the densifier. There, twin counter-rotating screws compact the material. Pressure and shear forces raise its temperature to between 380 and 390°F and forces it out a die. Water vaporizes during the process, resulting in final moisture content lower than 2%.
Unlike conventional batch-fed tub densifiers, which can be slow, inefficient and dangerous to operate, PES densifiers reduce labor requirements, energy consumption and maintenance costs while processing more product.
The densifier produces thick strands of homogeneous material that can be fed directly into a conventional extruder to form finished shapes. The strands also can be size-reduced in a standard granulator and the resulting regrind can be reprocessed or sold as high value recyclate.
Throughput is highly dependent on the characteristics of the input material and requirements for the final product. However, when processing plastic scrap that is relatively uniform in particle size, with a density of about 10-14 lb/ft³ and moisture levels below 15%, the PES model 600 has a nominal throughput of up to 3300 lb/hr.
The PES densifier is designed to operate under heavy loads, so all components are manufactured for strength and sturdiness. Operating forces are well balanced, and the main drive motor is generously oversized in order to maintain the production rates even in the presence of more “difficult” material. Under normal conditions, the motor runs at only about 60% of its maximum capacity. The PLC control system monitors several parameters continuously, including electrical power consumption and temperature of the extruded material, so that operation can be adjusted accordingly.
Please wait while flipbook is loading. For more related info, FAQs and issues please refer to DearFlip WordPress Flipbook Plugin Help documentation.
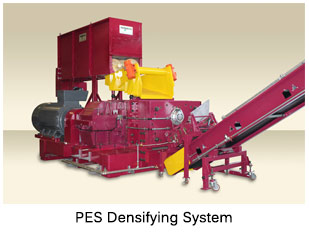
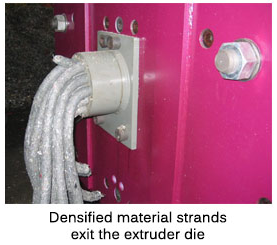
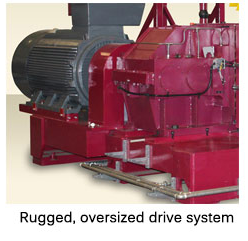
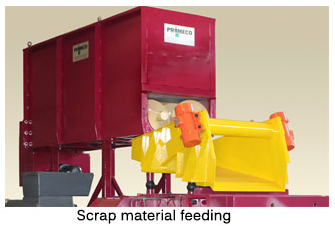
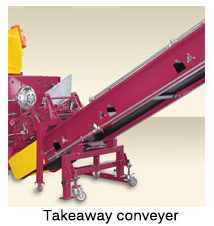